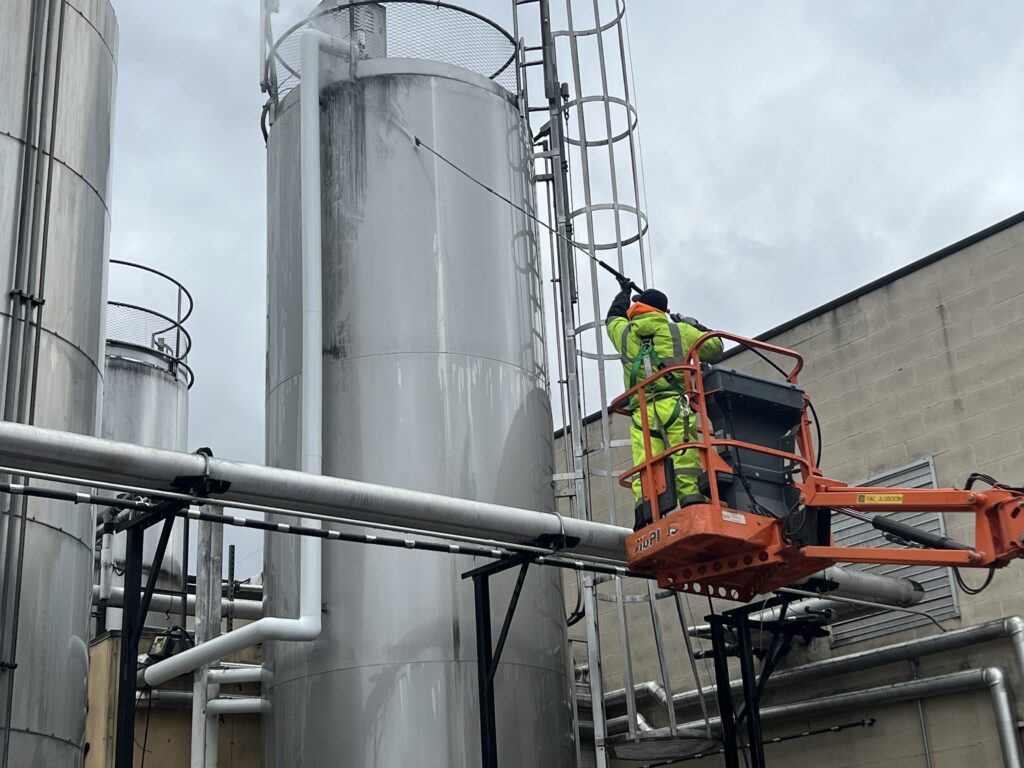
Storage silos play a crucial role across diverse industries like agriculture, food processing, and pharmaceuticals, demanding diligent maintenance to safeguard stored material quality, operational efficiency, and safety standards. One essential practice in maintaining these storage units is pressure washing. This article explores the various reasons why pressure washing is critical to silo maintenance, outlining key benefits, risks of neglect, and manufacturer recommendations supported by industry standards and guidance from major silo manufacturers.
The Key Benefits of Pressure Washing Storage Silos
- Prevention of Contamination and Enhanced Hygiene Silos used for organic materials, grains, animal feed, or certain chemicals are particularly prone to contamination. Over time, residues and biological contaminants (like mold, bacteria, and fungi) can build up, posing risks to product safety. Routine pressure washing removes these residues, preventing cross-contamination and maintaining sanitary conditions crucial for industries with strict hygiene requirements, such as food and beverage processing.Source Recommendation: According to the Grain Elevator and Processing Society (GEAPS), regular cleaning of storage facilities, especially those handling food products, is essential for mitigating contamination risks and ensuring regulatory compliance across the food supply chain [1].
- Improved Product Quality and Safety In industries handling consumables or pharmaceuticals, maintaining a contaminant-free environment is paramount. Pressure washing eliminates old residues, supporting product integrity and preventing cross-contamination. For example, in grain or dairy product storage, mold and bacterial growth can lead to product spoilage if silos are not cleaned consistently. Pressure washing silos storing sensitive materials ensures that each batch meets industry standards for purity and quality.
- Maintaining Structural Integrity and Equipment Longevity Over time, residue accumulation can weaken silo materials, particularly metals prone to rust or corrosion. Many manufacturers recommend pressure washing to avoid harmful deposits that lead to corrosion. For instance, residues can hold acidic or corrosive substances that compromise metal linings. Removing these buildups preserves the structural integrity of the silo, reducing the need for costly repairs and extending the lifespan of these essential storage assets.Manufacturer Recommendation: Flexicon Corporation, a major supplier of storage and handling systems, emphasizes that regular washing reduces corrosion risks and supports the longevity of stainless and galvanized steel silos used in industrial applications [2].
- Efficient Operations and Reduced Downtime Unclean silos can lead to clogs, reducing material flow rates and slowing down production processes. Residue build-up can block valves and other discharge points, resulting in costly downtime. Regular pressure washing removes these potential blockages, ensuring materials move freely and allowing for smoother, more efficient operations. In high-frequency production settings, this improved flow can translate to significant operational savings.Source Recommendation: AGI, a leading manufacturer of storage solutions, highlights that proactive maintenance, including pressure washing, enhances operational efficiency and mitigates unexpected disruptions caused by material blockages [3].
- Compliance with Industry Standards and Safety Regulations Regulatory agencies, including the FDA and OSHA, often have stringent cleanliness requirements for storage facilities to prevent contamination and safety risks. Inspections can lead to penalties if silos fail to meet these standards. For example, the FDA mandates high sanitation standards for food-related facilities, while OSHA oversees general safety compliance in handling volatile or combustible materials. Pressure washing helps facilities stay compliant, avoiding fines and safeguarding the company’s reputation.Source Recommendation: The American Society of Agricultural and Biological Engineers (ASABE) provides guidelines for storage maintenance practices, underscoring the need for regular pressure washing to uphold safety and compliance across industries that store food and industrial materials [4].
- Fire and Combustion Hazard Prevention For materials like grain or powdered chemicals, dust buildup in silos presents a significant fire hazard. Combustible particles can form explosive atmospheres when airborne, especially if exposed to heat or static electricity. Pressure washing removes these fine particles, significantly lowering the risk of fires or explosions, a critical concern for sectors like agriculture and milling.Source Recommendation: The National Fire Protection Association (NFPA) suggests a strict maintenance schedule, including pressure washing, to mitigate fire risks associated with combustible dust in storage facilities [5].
Manufacturer Recommendations for Optimal Silo Pressure Washing
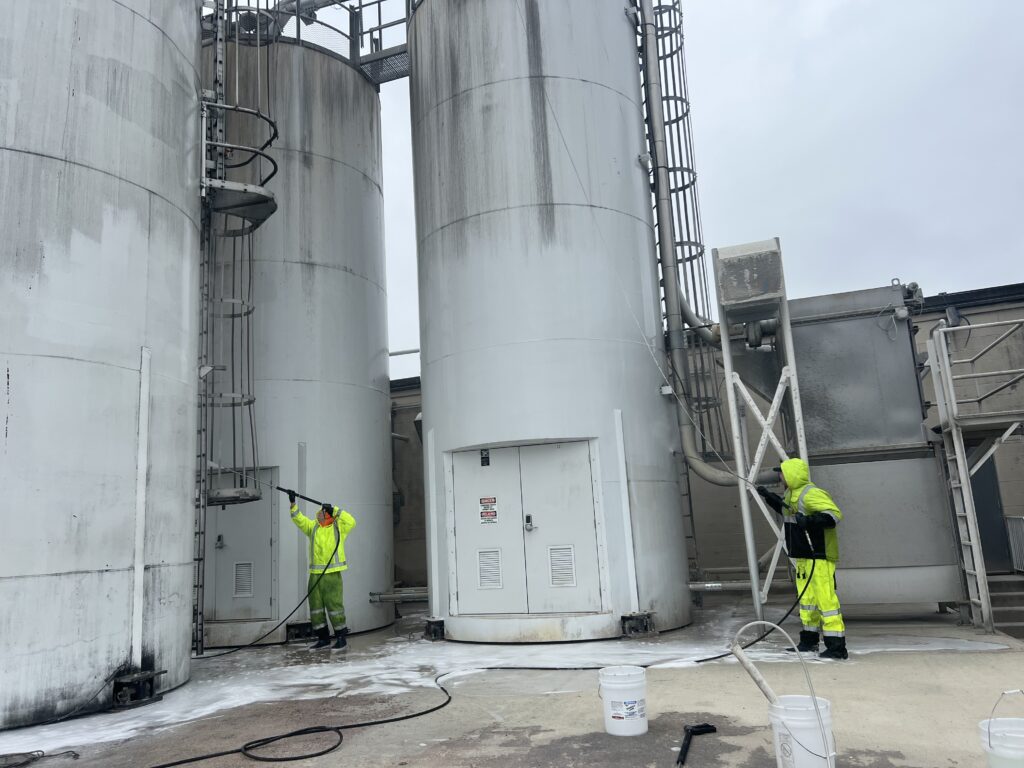
Silo manufacturers such as Flexicon, Meridian Manufacturing, and AGI recommend specific protocols to achieve the best results in pressure washing while safeguarding silo integrity. Here are the essential guidelines derived from industry leaders:
- Pressure Levels and Nozzle Settings Many manufacturers recommend pressure levels between 2000 and 4000 PSI for cleaning silos. High-pressure settings are effective for heavy residues but should be applied with care to prevent damage to protective linings. Fan or rotary nozzles are typically suggested for even pressure distribution and to avoid over-concentrating pressure in one area.Manufacturer Guidance: Flexicon Corporation advises using moderate PSI settings and choosing appropriate nozzle types to ensure comprehensive cleaning without causing internal damage to steel or plastic-lined silos [2].
- Water Temperature Considerations For removing organic residues, water temperatures between 100-120°F are usually recommended by manufacturers. However, sensitive materials like certain coatings may only withstand cooler water temperatures. For this reason, it’s essential to follow silo-specific temperature recommendations to avoid damage to protective coatings.Manufacturer Guidance: AGI recommends water temperature ranges based on the type of stored material and interior lining of the silo, which helps remove residue without degrading materials [3].
- Cleaning Frequency for Optimal Results While general cleaning frequency recommendations suggest biannual or quarterly pressure washing, many manufacturers advise monthly cleaning for silos in high-use settings, particularly in food or chemical storage where contamination risks are higher. Consistent cleaning prevents build-ups that would otherwise require extensive cleaning or costly repairs.
- Chemical Use in Pressure Washing Manufacturers caution against harsh chemicals, which can damage internal linings. Eco-friendly, food-safe cleaning agents are typically recommended, particularly in food-grade applications. For more demanding residue, manufacturers may suggest mild detergents but warn that these should be used sparingly to avoid degradation of linings.Source Recommendation: Meridian Manufacturing emphasizes the importance of using safe cleaning agents that align with their products’ chemical tolerance levels to avoid premature wear on surfaces [6].
- Hiring Professional Cleaning Services Large silos or complex structures may require professional cleaning services that can adhere to manufacturer guidelines and industry standards. Professional services offer specialized tools, such as high-reach washers and adaptable nozzles, to provide thorough, careful cleaning that maintains equipment longevity.
Conclusion
- Prevention of Contamination and Product Quality: Pressure washing reduces contamination, maintains quality, and supports regulatory compliance.
- Structural Integrity and Equipment Life: Routine cleaning extends silo life by preventing rust and corrosion.
- Efficiency and Reduced Downtime: Clean silos enhance material flow, leading to improved operational efficiency.
- Regulatory Compliance: Pressure washing helps meet industry health and safety standards, reducing the risk of non-compliance.
- Fire Prevention: Removing dust buildup reduces fire risks associated with combustible storage materials.
By following a regular pressure washing routine, companies not only comply with industry standards but also benefit from prolonged silo performance, reduced contamination risks, and enhanced safety. Manufacturer-backed recommendations provide effective guidance, ensuring that silos remain in optimal condition and serve their intended purpose for years to come.
References
- Grain Elevator and Processing Society. (GEAPS). “Storage Facility Maintenance for Contamination Control.”
- Flexicon Corporation. “Maintenance Recommendations for Industrial Storage and Handling Systems.”
- AGI, Agricultural Growth International. “Operational Best Practices for Silo Efficiency.”
- American Society of Agricultural and Biological Engineers (ASABE). “Guidelines for Agricultural Storage Maintenance.”
- National Fire Protection Association (NFPA). “Dust Hazard Prevention in Storage Facilities.”
- Meridian Manufacturing. “Recommendations for Cleaning and Maintenance of Agricultural Silos.”
By adhering to these best practices and guidelines, companies can ensure the safety, efficiency, and longevity of their storage silos, ultimately supporting product quality and compliance across industries.